Steel Rail Knowledge That Is Less Well Known by People
1. Function and Basic Requirements of Railroad Train Track
(1) Basic requirements of railroad train track
Basic requirements of railroad train track include strength, stiffness, hardness, toughness, weldability and economics.
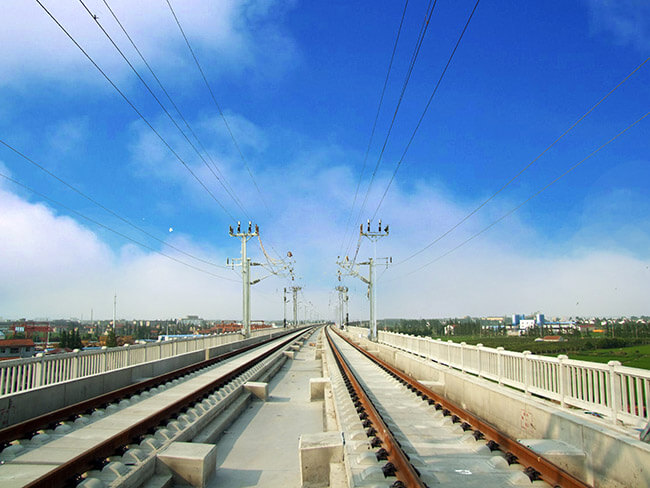
(2) Function, type and section of railroad train track
A. There are five main functions of railroad train track, including train wheels supporting, direction guiding, outside force transferring (to bear force from wheels and transfer to the sleepers), providing continuous, smooth and minimal surface resistance to the wheels and electric conduction.
B. railroad train track can be divided into different types according to different methods. First, as for rail weight, it can be classified into 43kg/m, 50kg/m, 60kg/m, 75kg/m, etc. Second, as for railroad train track length, it can be classified into tandard rail and short rail. Third, as for railroad train track material, it can be classified into carbon rail, alloy rail and heat reatment rail. Fourth, as for railroad train track strength, it can be classified into domestic rail, import rail andtest rail.
C. railroad train track section is in the shape of “T” which has the best function of bending resistance. Seen from the section drawing, we can easily recognize that rail consists of three parts of rail head, railroad train track web and foot. Rail head is the place of contacting with wheels, which must be so big and thick that it can bear huge pressure. Rail web shall be thick and high enough to meet the requirements of bearing, bending resistance and connecting. Rail foot plays an important role in maintaining stability of rail.
Four main parameters of railroad train track section: H, B, b, t. In order to guarantee the stability, the ratio of H:B shall be 1.15-1.2. To ensure uniform rolling cooling, reasonable proportion of rail must be achieved.
2. Material and Mechanical Performance of Railway Steel Rail
Material and mechanical performance of railway steel rail depend on chemical composition, metal structure and heat treatment process.
(1) Chemical composition of railway steel rail
Rail steel is composed of a number of main chemical elements which are Fe, C, Mn, Si, P, S, etc.
A. If C increased, tensile strength, abrasion resistance and hardness of rail steel shall also increase but toughness decrease.
B. If Mn increased, tensile strength and toughness of rail steel shall also increase. If removing iron and sulfur, high manganese steel shall have good wear resistance.
C. If Si is combined with O, rail steel shall remove bubbles and increase density. If Si is increased, rail steel shall have good wear resistance.
D. P makes rail steel have cold brittleness.
E. S does not dissolve in Fe, which exists in form of iron sulfide, it makes rail steel have hot brittleness.
(2) Mechanical performance of railway steel rail
Mechanical properties of rail steel include strength limitationσb, yield limitationσs, fatigue limitationσr, elongationδ5, section shrinkageψ, toughnessαh and hardness.
(3) Strengthening technology of railway steel rail
A. Steel rails alloying
When alloying elements of Mn, Si and Cr are added into steel, the rail shall get overall strengthening with uniform surface hardness and good welding performance.
B. Heat treatment of steel rails
Due to huge impact on rail joint, rail head of rail end at the range of 30-70mm long shall have the quenching treatment to improve wear resistance.
Full-length quenching of rail: electric induction heating will accelerate the transformation of steel from austenite to perlite, which can improve its strength and toughness.
C. Steel rails alloying combined with heat treatment
3. Steel Rail Failure and Proper Use
(1) Steel rail failure
Steel rail failure is to influence and restrict performance of rail in use, for example, breaking, cracking and the others. According to the locations, appearance and reason of the failure shown on rail section, steel rail failure can be classified into 9 categories and further divided into 32 types.
A. Steel rail breaking
Rail breaking includes the following cases: first, the cross section of rail breaks into two parts at least; second, the crack has been through the section of rail head or rail foot; third, spalling of top surface of rail is >50(30)mm long and >10(5)mm deep in size.
Rail breaking directly threatens train safety. When any of the above cases occurs, the best choice is to replace the rail in time.
B. Steel rail cracking
Steel rail cracking is formed by certain part of rail material’s separating from the rail except rail breaking.
C. Steel rail wear
First, vertical wear
Vertical wear occurs on the rails of all types of lines, especially on the direct lines and the big curve of track. With axle load and total weight of train increase, vertical wear will become more serious when track geometry is set incorrectly.
Second, side wear
Side wear is caused by wheel friction and wheel sliding.
Third, corrugated wear
Corrugated wear occurs on the top surface of rail with wavy uneven or crushing cracks.
Allowable limitation of rail wear depends on strength condition and structural condition. It contains as below: first, enough strength and bending resistance stiffness; second, wheel flange can’t contact with rail joint under the worst condition; third, corrugated wear rail will not cause damage of track and increase of maintenance workload.
(2) Proper use
Proper use of rail is that reasonable use period of the rail shall be determined, the rail shall be used by classification system and the old rails shall be repaired periodically based on the analysis of the comprehensive economic benefit.
A. Using the steel rail by classification
Rail shall be used twice or multiple times. For inside and outside curve rails, or curve and straight rails, they can replace one another to use.
B. Steel rail maintenance technology
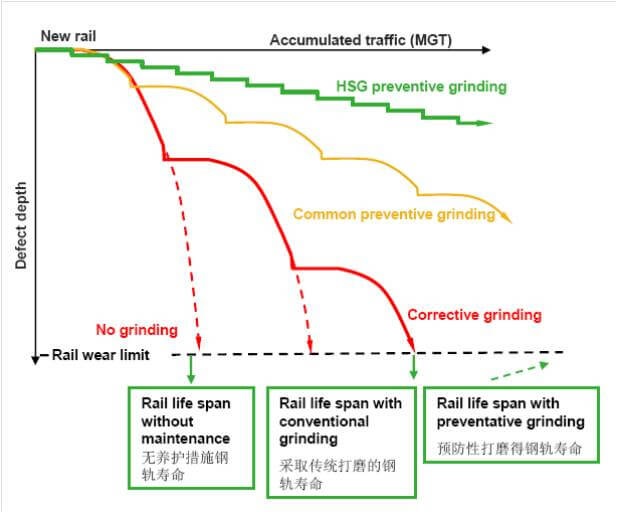
First, steel rail grinding
Steel rail grinding is to grind rail to be smooth and flat by grinding machine after removing uneven surface abrasion, spalling, etc. It can be divided into three categories according to the grinding purpose and depth including maintenance grinding, preventive grinding and section (outline) grinding.
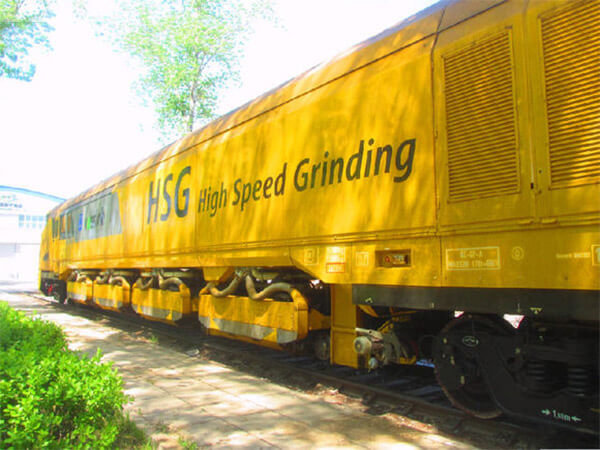
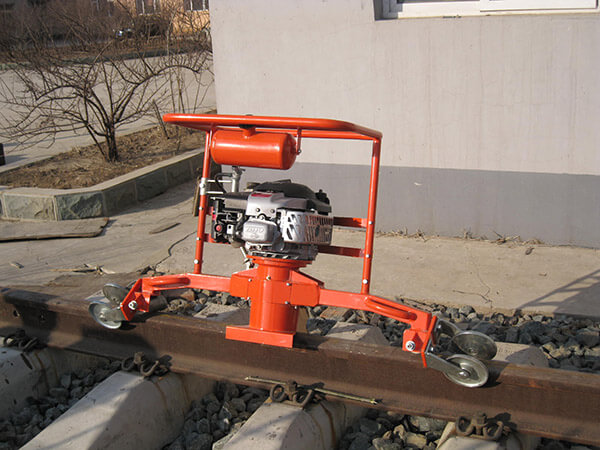
Second, steel rail welding
When damages from uneven abrasion, spalling or wheel burn are about 1mm deep, steel rail welding shall be done in time.
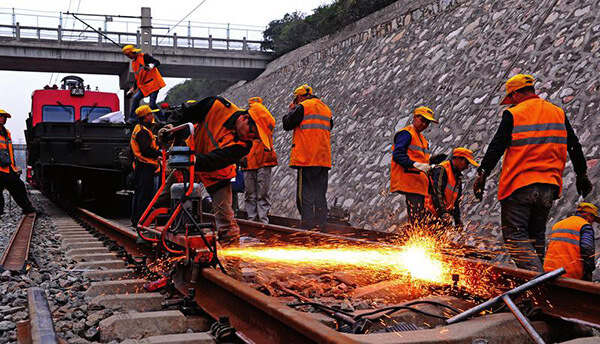
4. The Main Failure of High-speed Rail
High-speed train runs at high speed with light axle load and relatively small abrasion in vertical and horizontal directions, so contact fatigue damage of rail are major problem which includes rail head creaking, hidden defect and honeycomb cracking.
5. Steel Material of High-speed Rail
Steel material for high-speed rail must meet the requirements of strength-toughness matching, purity, excellent welding and so on. The steels of UIC900A, U71Mn and PD3 are suitable for high-speed rail.
6. Construction of the 100m Long Rail Laying
Construction of the 100m long rail laying is to be done as below:
A. Using 10 sets of portal jib cranes, the 100m long rails are hoisted directly to train flat car on which rails are laid down seven layers with 16 pieces each, every layer is fixed by the lock in the middle and put isolation device between layers to prevent lateral movement.
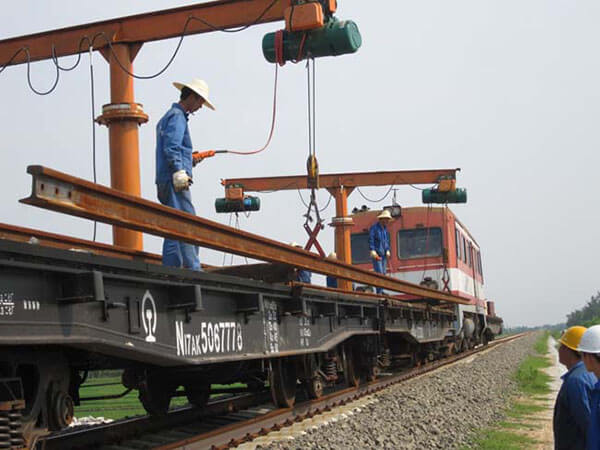
B. Temporary storage generally should be pushed to the No-catenary for lifting and unloading. The 10 sets of 3tons movable portal jib cranes work synchronously ups and downs. Square wood at intervals of 5m is used as the isolated storage. Long rail locking device adopts bolt combined with steel plate.
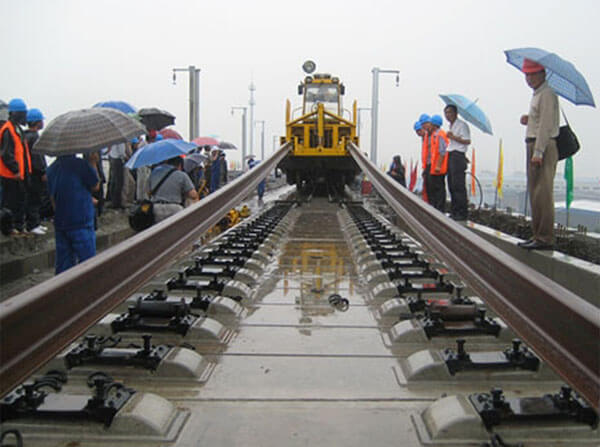
C. Long rail car will push 100m length steel rails to the front site where to lay rail on non-ballasted track. There are rollers placed on track slab at intervals of 10m, the machine of artificial channeling steel rails will send long rails directly to the rollers. Workers with crowbars walk forward following the front of long rail to raise rail head to avoid running down the roller and bruising track slab. When pushing process is completed, remove the rollers, and install rails on tie plates with bolts and fasteners screwing to proper torsion using electric and manual wrench in accordance with the requirements of construction specifications. In order to prevent the screw rust and improve insulation performance, bolts and fasteners should be coated with oil.
We receive enquiries in English, Español (Spanish), Русский язык (Russian), Français (French) and العربية (Arabic). Our professional team will reply to you within one business day. Please feel free to contact us!